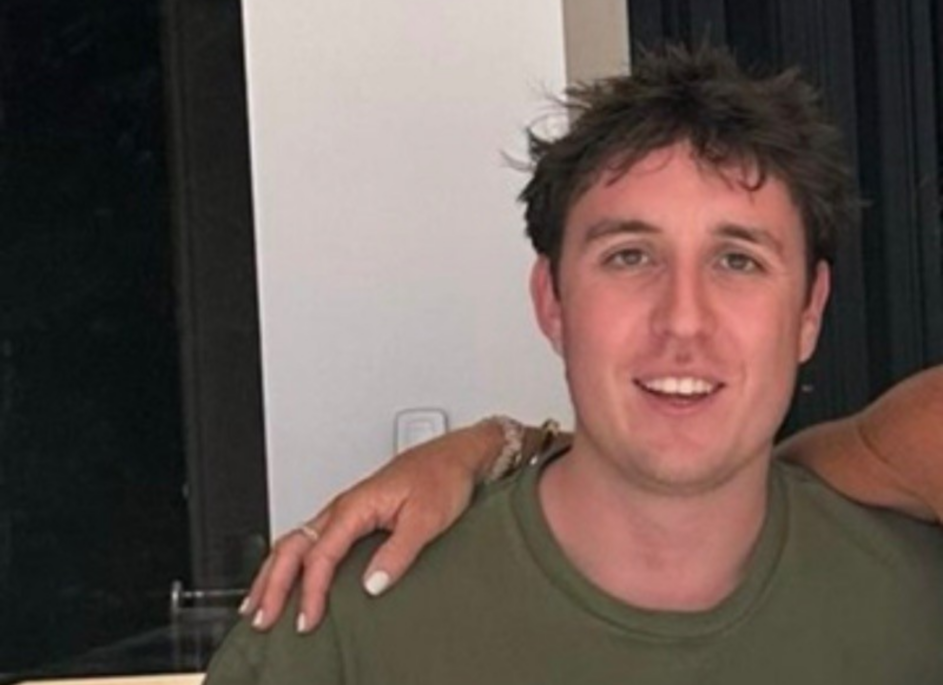
Hi, I’m Freddie, a 22-year-old graduate and this blog is your VIP pass to my wild ride at Renegade Brewery. Read on for the unique perspective of someone with no prior experience, going behind the scenes at Renegade.
The purpose of this is to outline my experiences, and the typical daily tasks encountered by someone working in a brewery. I’ll highlight six key lessons I’ve learned, as well as candid thoughts on my time in at Renegade.
Delivery driving:
Each morning the drivers are loaded up and sent out using Optima route, a self-guided navigation system which they can follow in order to complete the required drops and pick-ups required. Spending a day in the van myself I could really see how time efficient they need to be in their deliveries. Their reliability on this software is what enables them to have the efficiency they have.
Deliveries:
The first thing I witnessed in the warehouse was the influx of deliveries the warehouse operatives take in and sort through. Over the course of the day I would estimate there were deliveries around every 20 mins. I spent most of the time observing the process being implemented from the moment the deliveries are signed for and officially become part of our inventory; through to the process of cataloguing them. Luckily due to the effectiveness of modern technology this can be done efficiently by the Fulfilment Manager through the use of a software called SAP Business One.
Stock processing/monitoring:
This role is vital in the warehouse. Once new stock is added, it must be processed and monitored to keep other departments updated on availability, location, and viability. Stock is usually ordered as needed, but surplus requires quantity adjustments for new brews. Continuous stock maintenance ensures the business runs efficiently.
Orders:
An increase in deliveries is coupled with a high volume of orders needing quick processing. Weekend online orders often include a variety of items like t-shirts, hoodies, and exclusive holiday Christmas boxes. The warehouse team must efficiently prepare, package, and dispatch these orders. For Christmas boxes, customers can choose between a four-pack of 440ml bottles with a glass tumbler or a three-bottle gift pack. Hundreds of handcrafted orders are received each season, reflecting the significant effort behind the scenes.
Week 2:
The Lab: The Lab serves as the heart of the brewery, where all beer testing occurs. Although it’s compact and situated next to the main brewing area, this space is essential for managing and documenting all necessary information related to the beer. A primary function of the lab is to test fermentation levels and carbon dioxide, among other factors, ensuring the quality of various products, including lager, bitter, and non-alcoholic options. This guarantees that everything meets the highest standards, preventing any potential issues.
Brewing:
The Idea of brewing beer from someone with limited experience, was thought to be quite a straightforward process. Brewing beer may seem simple at first, but it involves complex processes. It starts in the mill room, where unique recipes are crafted based on specific grains and malts. These ingredients are measured in kilograms and added to the milling machine.
After this stage, the process becomes largely automated. It’s fascinating to see how the grain ferments under the right conditions, with precise measurements being critical. Experienced specialists monitor the brewing closely. Once fermentation is complete, the beer undergoes a final quality check before packaging.
Packaging:
The bottling system is one of the most intricate aspects of the beer production process. The level of precision maintained throughout is remarkable. The bottles arrive at the production line as empty shells, ready for processing. The first step involves sorting them and preparing them for a processing machine that can handle up to 1.9 bottles per second, equating to about six to seven thousand bottles an hour! Once sorted, labels are meticulously applied; anything that falls short of perfection is discarded. Next, the beer is filled into the bottles, and they are sealed. After sealing, the bottles pass through a counting machine to ensure that everything has been filled in the correct quantities. Finally, they proceed to the packaging system, where they are packaged according to whether they are bottles or cans, ready for collection and shipment by the warehouse.
Cleaning:
The cornerstone of Brewery operations, cleaning is undoubtedly the most crucial aspect to prioritize within a brewery. A clean and sanitized work environment is essential for the smooth functioning of any brewery. Any contamination could lead to catastrophic consequences, and if not addressed swiftly and effectively, the repercussions could be devastating. Fortunately, this is managed through ongoing cleaning practices. As observed first hand, every tank and pipe undergoes a thorough cleaning process immediately after use, ensuring that the risk of contamination is eliminated and the brewing environment remains safe.
General Maintenance:
Anticipating that things may not go as planned is crucial in a brewery, where many components must work together seamlessly. Issues like CO2 tank bursts, pressure loss, water shortages, or bottling system breakdowns can arise, making adaptability essential for technicians. Their ability to handle these challenges effectively underscores the importance of prior experience for maintaining smooth brewery operations.
Week 3: The Final week
Marketing:
During my last week, I spent time with the marketing team. Observing their successful strategies to enhance a small brewery and help it thrive has been truly inspiring. Attending meetings and witnessing how they adapt and collaborate to tackle new daily challenges has been an intriguing experience. It also highlights the importance of effective communication and proper delegation in building upon their existing foundations while striving to achieve their ambitious future goals.
Sales:
Only witnessing the sales team for a brief period, was all I needed to see in the effectiveness that they bring to the table.
My time with the sales team focused on observing their operations. My past sales experience taught me that successful selling is about 90% connecting with the customer and only 10% about the product. During my day in London, I visited clients to address their queries and encourage reorders of Renegade products. Later, I recruited potential clients by visiting promising pubs, introducing ourselves, and offering free samples. This experience helped me develop valuable interpersonal skills.
6 Key Things I’ve Learnt:
Yes, they might sound generic, but these are some of the things that I’m taking away from my time at Renegade:
- Organisational and Communicational skills are the key to success.
- The more work you put in the better your results.
- Wow! There is a lot of cleaning involved in brewing…. nothing can be too clean.
- When accidents happen and things go wrong, which they will, there is always a work around and something else to be done.
- Having guidelines is good but having the freedom to explore and freelance in your own way, on your own ideas is the key to a successful unique result.
- Use whatever is given to you and make it into something better.
My final opinion:
Beginning this internship with no expectation of what was going to happen, has been a truly unique experience. It has allowed me to engross myself in the life that occurs here at renegade and try to develop myself as much as possible within that time period, through watching the various teams I’ve had the privilege of meeting and observing.
I believe I have gained a wealth of knowledge from this experience, particularly in areas like responsibility, reliability, and much more. However, one lesson stands out to me as someone without prior experience: for a company to succeed, it’s essential to surround yourself with individuals who share the same values and aspirations. This collective alignment fosters a common goal, such as the ongoing growth and development of Renegade. Over the past few weeks, I have come to realize that the creation of unity is the most vital lesson I have learned.
I just want to say a huge thank you to all those at Renegade brewery that have taken the time and the effort for giving me the opportunity to share with me their lessons and things they have learnt in order to help me continue onwards.